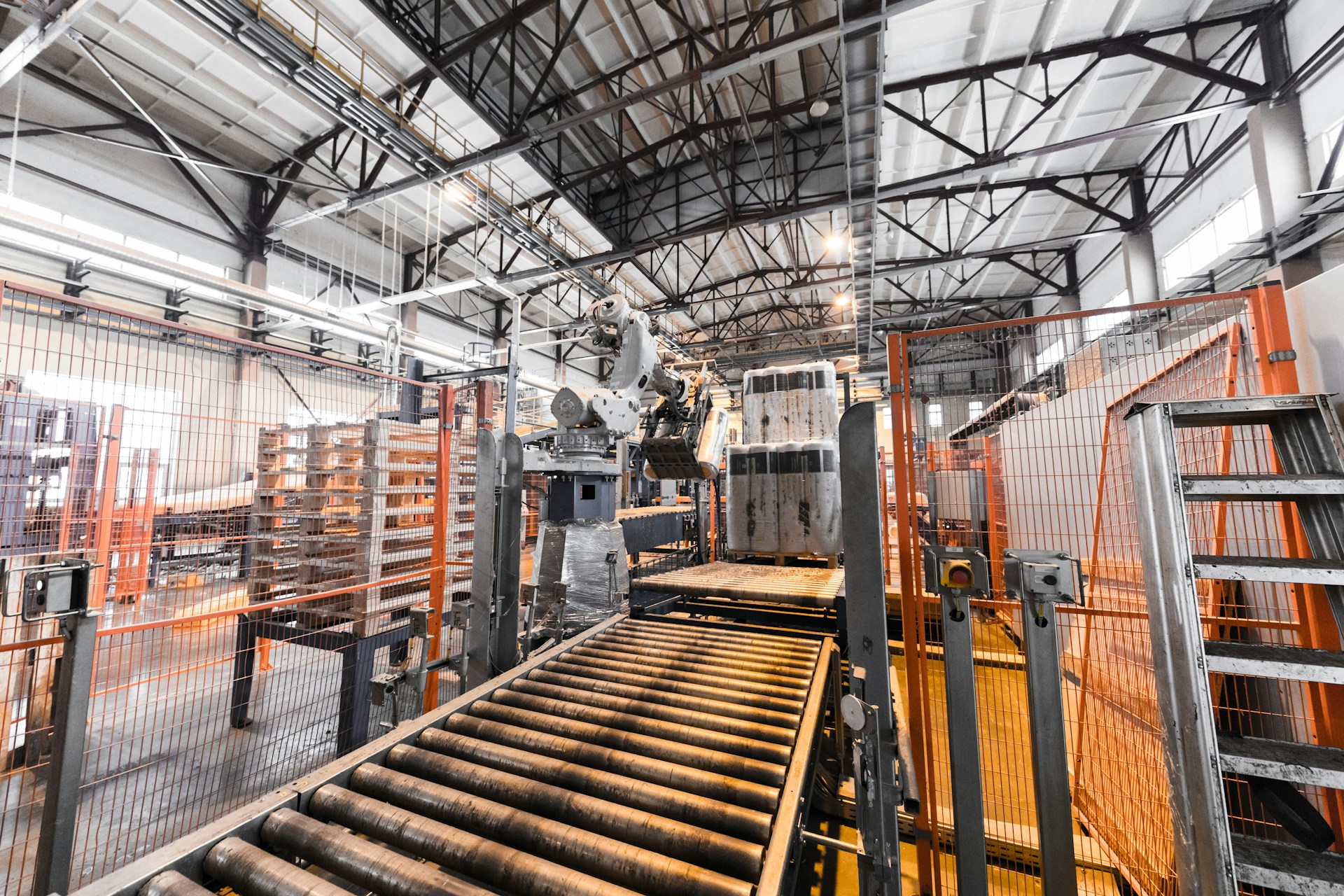
Downtime is expensive. When a conveyor system stops, everything behind it does too. Production slows, output drops, and costs go up fast. And in many industrial setups, it all comes down to one surprisingly small part: the conveyor belt scraper. Sounds minor, right? But this one component has a huge role in keeping systems running smoothly.
Contents
- 1 Why Material Buildup Is a Real Problem
- 2 The Scraper’s Role in Preventing All That
- 3 What Happens When You Don’t Use One?
- 4 Not All Scrapers Are Equal
- 5 Scrapers = Efficiency Boosters
- 6 Maintenance Teams Love Them (When They Work)
- 7 How to Keep Your Scrapers Doing Their Job
- 8 Keep the System Running Smoothly
Why Material Buildup Is a Real Problem
In any bulk handling operation, there’s spillage. Fine dust, sticky residue, and chunks of material… they don’t always stay where they’re supposed to. Without a scraper doing its job, leftover material sticks to the return side of the belt. This can lead to:
- Misalignment
- Roller damage
- Belt wear
- Build-up on pulleys
- Safety hazards from debris
Over time, even a small amount of carryback can snowball into something bigger. Once material starts accumulating, it affects performance across the whole system. Belts start slipping. Components get blocked. Sensors can trigger false alerts or shut things down entirely.
The Scraper’s Role in Preventing All That
A belt scraper’s job is straightforward: remove leftover material from the belt before it circles back through the system. But the impact of doing that job well? Massive. Here’s what a properly fitted conveyor belt scraper does for your system:
- Reduces carryback – Keeps loose material from returning into the system
- Prevents belt mistracking – Helps belts stay aligned and centred
- Protects components – Minimises wear on rollers, pulleys and seals
- Improves safety – Cuts down on material build-up that can become a slip or fire hazard
- Lowers maintenance costs – Less buildup means fewer breakdowns and callouts
- Increases uptime – A clean belt = a smoother-running system
What Happens When You Don’t Use One?
Short answer: problems stack up. A common issue is seized rollers. Material left on the return belt often falls off underneath, building up around the bottom rollers. That material hardens or gets sticky, jamming the roller until it locks up. From there, things escalate: rollers overheat, belts get damaged, and before you know it, you’re looking at a full stop and a repair job. It doesn’t take long for one missed scraper to cost hours of downtime. And depending on the industry, that downtime can cost thousands.
Not All Scrapers Are Equal
The basic idea of a scraper is simple. But in practice, you’ve got to get a few things right for it to work properly.
Material choice matters. Too soft, and it won’t clean effectively. Too hard, and it’ll wear down the belt. Different applications call for different types, whether it’s a polyurethane blade for light materials or tungsten tips for tough, abrasive loads.
Placement is critical. Primary scrapers go right at the head pulley to tackle most of the material. Secondary scrapers sit just behind and catch anything left behind. Miss one, and your system’s not fully protected.
Tension and pressure need regular checks. A loose or worn scraper won’t do the job. And if it presses too hard, it causes belt wear. It’s all about finding the right balance.
Scrapers = Efficiency Boosters
Think about what happens when everything runs clean:
- Belts glide with less resistance
- Bearings and pulleys last longer
- There’s less need to pause production for clean-up
- Operators spend less time on manual checks and fixes
In systems where productivity and reliability are everything, those small gains add up. That’s why scrapers aren’t just a maintenance item, they’re part of the overall efficiency strategy.
They help keep systems running at their best without interruption. That translates to faster production, fewer repair costs, and less downtime.
Maintenance Teams Love Them (When They Work)
No one enjoys having to climb into a dusty chute or under a belt to clean off built-up material. It’s time-consuming, sometimes risky, and always annoying. Scrapers, when properly installed and maintained, take care of most of that work automatically.
They don’t eliminate maintenance, but they reduce the amount needed. Instead of cleaning out clogged rollers or replacing damaged belts, crews can focus on proactive maintenance instead of putting out fires. And that’s a better use of time and budget across the board.
How to Keep Your Scrapers Doing Their Job
Even the best scraper won’t work forever without attention. To make sure it keeps doing its job, regular checks are a must. Here’s what to look for:
- Blade wear – Replace when the edge is rounded or worn down
- Tension settings – Adjust to maintain consistent contact with the belt
- Mounting brackets – Make sure they haven’t come loose or shifted
- Buildup behind the blade – Clean out anything that’s gotten stuck
- Compatibility – Reassess if materials or belt speed have changed
Setting up a simple inspection schedule, weekly or monthly depending on usage, can make a big difference. It’s quick, straightforward, and prevents bigger issues down the track.
Keep the System Running Smoothly
At the end of the day, conveyor belt scrapers are one of those things that, when they work, you barely notice. And that’s exactly the point.
Their job is to stay in the background, quietly keeping things clean and efficient. No alarms, no flashing lights—just consistent, reliable performance.
But take them for granted, and the consequences show up fast. From unexpected stoppages to major component damage, it can spiral quickly.
So while they might not seem like the most important part of your system, they’re one of the most effective ways to keep everything running as it should.
Leave a Reply
You must be logged in to post a comment.